How to maintain Atlas air compressor GA132VSD
The Atlas Copco GA132VSD is a reliable and high-performance air compressor, specifically designed for industrial applications that require continuous operation. Proper maintenance of the compressor ensures optimal performance, extended service life, and energy efficiency. Below is a comprehensive guide for the maintenance of the GA132VSD air compressor, along with its key technical parameters.
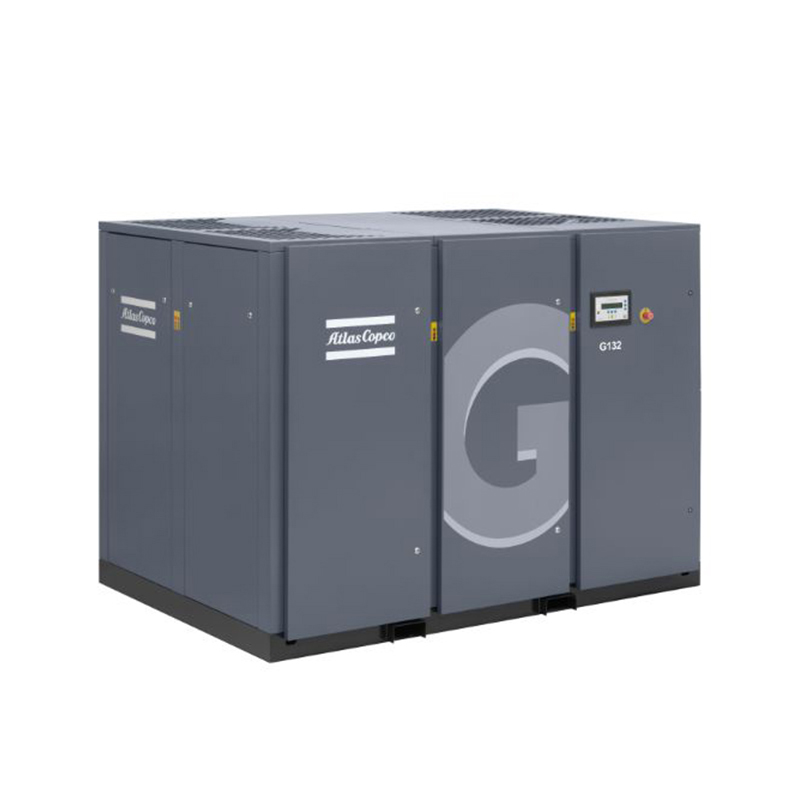
- Model: GA132VSD
- Power Rating: 132 kW (176 hp)
- Maximum Pressure: 13 bar (190 psi)
- Free Air Delivery (FAD): 22.7 m³/min (800 cfm) at 7 bar
- Motor Voltage: 400V, 3-phase, 50Hz
- Air Displacement: 26.3 m³/min (927 cfm) at 7 bar
- VSD (Variable Speed Drive): Yes, ensures energy efficiency by adjusting motor speed based on demand
- Noise Level: 68 dB(A) at 1 meter
- Weight: Approximately 3,500 kg (7,716 lbs)
- Dimensions: Length: 3,200 mm, Width: 1,250 mm, Height: 2,000 mm
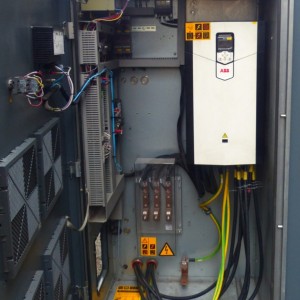
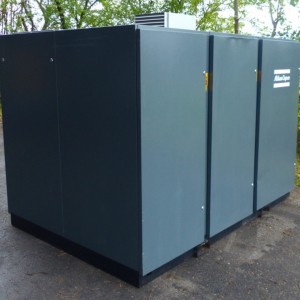
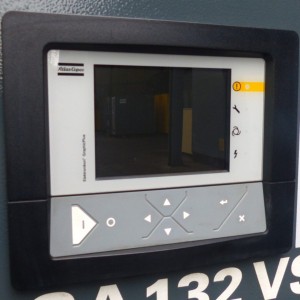
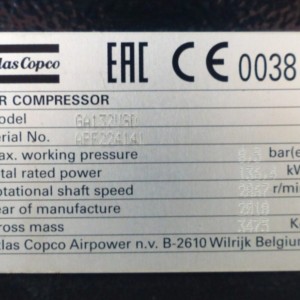
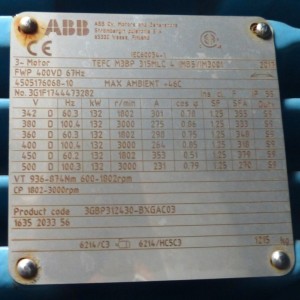
1. Daily Maintenance Checks
- Check the Oil Level: Ensure that the oil level in the compressor is adequate. Low oil levels can cause the compressor to run inefficiently and increase wear on critical components.
- Inspect the Air Filters: Clean or replace the intake filters to ensure unrestricted airflow. A clogged filter can reduce performance and increase energy consumption.
- Check for Leaks: Regularly inspect the compressor for any air, oil, or gas leaks. Leaks not only reduce performance but also cause safety hazards.
- Monitor the Operating Pressure: Verify that the compressor is operating at the correct pressure as indicated by the pressure gauge. Any deviation from the recommended operating pressure could indicate an issue.
2. Weekly Maintenance
- Inspect the VSD (Variable Speed Drive): Perform a quick inspection to check for any unusual noises or vibrations in the motor and drive system. These could indicate misalignment or wear.
- Clean the Cooling System: Check the cooling system, including the cooling fans and heat exchangers. Clean them to remove dirt and debris that could cause overheating.
- Check Condensate Drains: Ensure the condensate drains are functioning properly and free from blockages. This prevents the accumulation of water inside the compressor, which can cause rusting and damage.
3. Monthly Maintenance
- Replace Air Filters: Depending on the operational environment, air filters should be replaced or cleaned every month to prevent dirt and particles from entering the compressor. Regular cleaning extends the life of the filter and ensures better air quality.
- Check Oil Quality: Monitor the oil for any signs of contamination. If the oil appears dirty or sludgy, it’s time to change it. Use the recommended oil type as per the manufacturer's guidelines.
- Inspect Belts and Pulleys: Check the condition and tension of belts and pulleys. Tighten or replace any that appear worn or damaged.
4. Quarterly Maintenance
- Replace Oil Filters: The oil filter should be replaced every three months, or based on the manufacturer’s recommendations. A clogged filter can lead to poor lubrication and premature component wear.
- Check the Separator Elements: The oil-air separator elements should be checked and replaced every 1,000 operating hours or as recommended by the manufacturer. A clogged separator reduces compressor efficiency and increases operating costs.
- Inspect the Drive Motor: Check the motor windings and electrical connections. Ensure there is no corrosion or loose wiring that could cause electrical failures.
5. Annual Maintenance
- Complete Oil Change: Perform a full oil change at least once a year. Be sure to replace the oil filter during this process. This is crucial for maintaining the lubricating system’s effectiveness.
- Check the Pressure Relief Valve: Test the pressure relief valve to ensure it is functioning correctly. This is a critical safety feature of the compressor.
- Compressor Block Inspection: Inspect the compressor block for signs of wear or damage. Check for any unusual sounds during the operation, as this could indicate internal damage.
- Calibration of the Control System: Ensure the compressor’s control system and settings are calibrated according to the manufacturer's guidelines. Incorrect settings could impact energy efficiency and compressor performance.
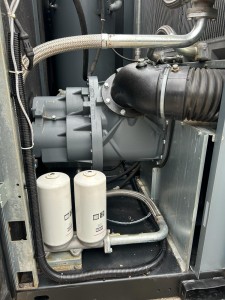
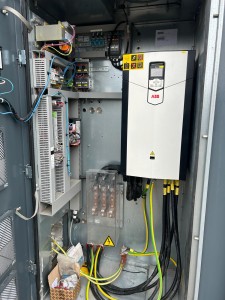
- Operate within Recommended Parameters: Ensure that the compressor is used within the specifications outlined in the manual, including operating pressure and temperature. Operating outside of these limits can lead to premature wear.
- Monitor Energy Consumption: The GA132VSD is designed for energy efficiency, but monitoring energy consumption regularly will help identify any inefficiencies in the system that need addressing.
- Avoid Overloading: Never overload the compressor or run it beyond its specified limits. This can cause overheating and damage to critical components.
- Proper Storage: If the compressor is not in use for a long period, make sure to store it in a dry, clean environment. Ensure that all parts are well-lubricated and protected from rust.
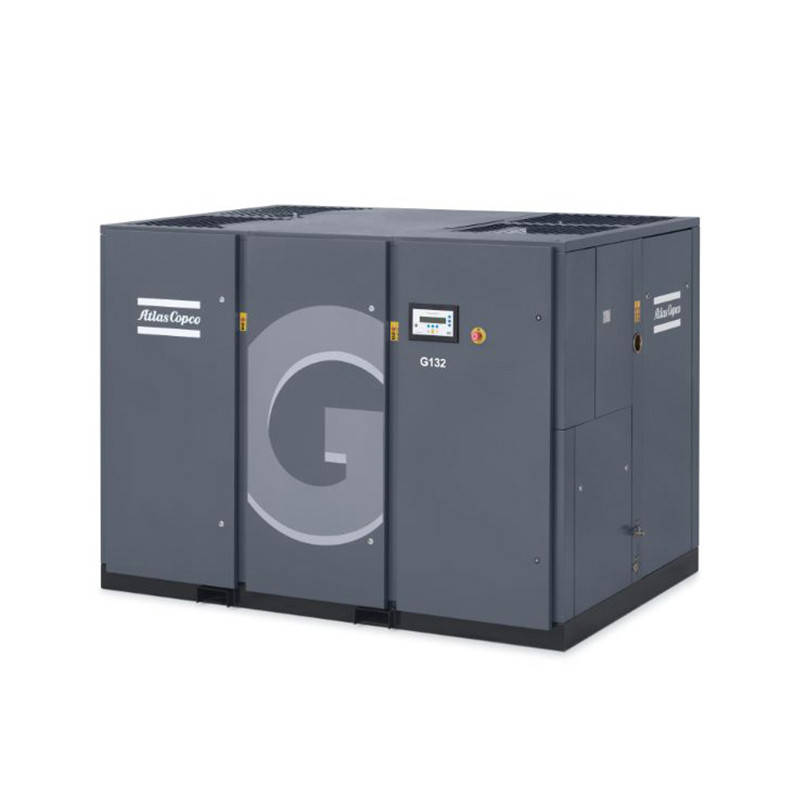
2205190474 | CYLINDER | 2205-1904-74 |
2205190475 | BUSH | 2205-1904-75 |
2205190476 | MINI.PRESSURE VALVE BODY | 2205-1904-76 |
2205190477 | THREADED ROD | 2205-1904-77 |
2205190478 | PANEL | 2205-1904-78 |
2205190479 | PANEL | 2205-1904-79 |
2205190500 | INLET FILTER COVER | 2205-1905-00 |
2205190503 | AFTER COOLER CORE UNIT | 2205-1905-03 |
2205190510 | AFTER COOLER-WITH WSD | 2205-1905-10 |
2205190530 | INLET FILTER SHELL | 2205-1905-30 |
2205190531 | FLANGE(AIRFILTER) | 2205-1905-31 |
2205190540 | FILTER HOUSING | 2205-1905-40 |
2205190545 | VESSEL SQL-CN | 2205-1905-45 |
2205190552 | PIPE FOR AIRFILTER 200-355 | 2205-1905-52 |
2205190556 | FAN D630 1.1KW 380V/50HZ | 2205-1905-56 |
2205190558 | VESSEL SQL-CN | 2205-1905-58 |
2205190565 | AFTER COOLER-WITH WSD | 2205-1905-65 |
2205190567 | AFTER COOLER CORE UNIT | 2205-1905-67 |
2205190569 | O.RING 325X7 FLUORORUBBER | 2205-1905-69 |
2205190581 | OIL COOLER-AIRCOOLING | 2205-1905-81 |
2205190582 | OIL COOLER-AIRCOOLING | 2205-1905-82 |
2205190583 | AFTER COOLER-AIRCOOLING NO WSD | 2205-1905-83 |
2205190589 | OIL COOLER-AIRCOOLING | 2205-1905-89 |
2205190590 | OIL COOLER-AIRCOOLING | 2205-1905-90 |
2205190591 | AFTER COOLER-AIRCOOLING NO WSD | 2205-1905-91 |
2205190593 | AIR PIPE | 2205-1905-93 |
2205190594 | OIL PIPE | 2205-1905-94 |
2205190595 | OIL PIPE | 2205-1905-95 |
2205190596 | OIL PIPE | 2205-1905-96 |
2205190598 | OIL PIPE | 2205-1905-98 |
2205190599 | OIL PIPE | 2205-1905-99 |
2205190600 | AIR INLET HOSE | 2205-1906-00 |
2205190602 | AIR DISCHARGE FLEXIBLE | 2205-1906-02 |
2205190603 | SCREW | 2205-1906-03 |
2205190604 | SCREW | 2205-1906-04 |
2205190605 | SCREW | 2205-1906-05 |
2205190606 | U-RING | 2205-1906-06 |
2205190614 | AIR INLET PIPE | 2205-1906-14 |
2205190617 | FLANGE | 2205-1906-17 |
2205190621 | NIPPLE | 2205-1906-21 |
2205190632 | AIR PIPE | 2205-1906-32 |
2205190633 | AIR PIPE | 2205-1906-33 |
2205190634 | AIR PIPE | 2205-1906-34 |
2205190635 | OIL PIPE | 2205-1906-35 |
2205190636 | WATER PIPE | 2205-1906-36 |
2205190637 | WATER PIPE | 2205-1906-37 |
2205190638 | WATER PIPE | 2205-1906-38 |
2205190639 | WATER PIPE | 2205-1906-39 |
2205190640 | FLANGE | 2205-1906-40 |
2205190641 | VALVE UNLADER CONNECTION | 2205-1906-41 |
Post time: Jan-03-2025