Atlas Copco Osc35 Osc355 Osc95
Oily water condensate—a poisonous mixture The air compression process has several by-products, one of which is a large volume of condensate. Generally, this condensate is an emulsified combination of oil and water that, if left untreated, is extremely harmful to the environment. Because of the potential damage this condensate can cause, strict regulations have been introduced that prohibit the disposal of such waste without rigorous treatment.
A clean solution for a dirty problem The Atlas Copco range of condensate separators is designed to separate the oil from the water, allowing for the water to be drained away and the oil to be disposed of in an environmentally friendly manner.
The unique OSD offers a condensate treatment package fully integrated into the compressor, reducing both installation costs and complexity. Clean water is discharged from the compressor outlet drain valves whilst the separated oil is collected in a generously sized oil can.
The unique OSD offers a condensate treatment package fully integrated into the compressor, reducing both installation costs and complexity. Clean water is discharged from the compressor outlet drain valves whilst the separated oil is collected in a generously sized oil can.
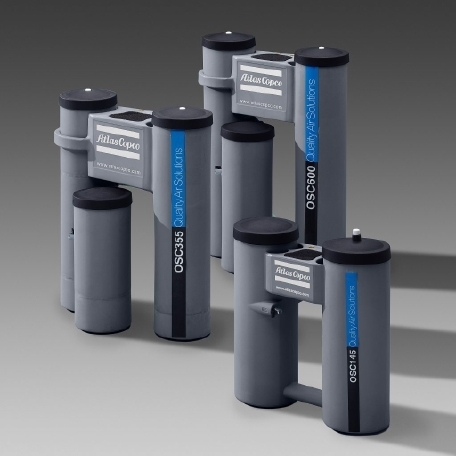
- High Efficiency and Energy Saving: The OSC series compressors are designed with a focus on energy saving, ensuring high output while minimizing energy consumption.
- Low Noise Design: Each model is equipped with low noise technology, ensuring that operations do not interfere with the working environment.
- Reliability: Made with high-quality materials and precision technology, ensuring long lifespan and high reliability.
- Easy Maintenance: The design is simple, reducing maintenance work and helping customers lower operating costs.
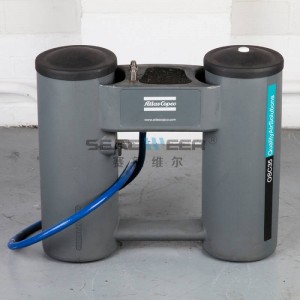
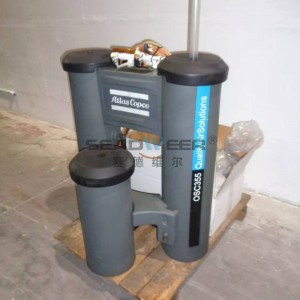
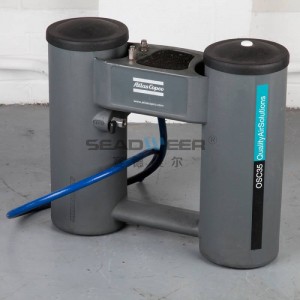
1 No standing or stagnant water means the elimination of health risks and a reduction in the need for frequent cleaning.
2 The unit’s design does not depend on gravitational separation, making it resistant to vibrations, shocks, and splashes. This results in improved and consistent performance, and there is no need for electronic "no loss drains" before the machine.
3 The condensate discharged contains minimal residual oil, allowing it to be safely drained without harming the environment or violating pollution standards.
4 The large-capacity chambers help prevent spillage in the event of a blockage or a sudden surge in inlet flow.
5 The system operates on filtration instead of relying on gravitational forces or weir separation, so oil density is no longer a crucial factor.

There's no need for an oil collection bottle, eliminating the risk of contaminating the separated condensate if the system experiences a failure.
It allows for the easy separation of multiple oil condensates
Poly-glycol condensate can be separated, although some reduction in unit capacity is required to ensure the filter's longevity.
The system is capable of separating most condensate emulsions
6 No reduction in capacity is needed for synthetic oil-based condensates, which simplifies model selection and allows for a smaller unit size, resulting in lower capital investment.
7 The advanced oleophilic filtration media guarantees consistent, reliable performance, prolongs the lifespan of the activated carbon and can eliminate all bacteria with an optional treatment.
8 The straightforward yet durable design ensures easy installation without the need for specialized setup and allows for quick, simple, and clean filter replacement.
9 The maintenance indicator provides an accurate alert when the filter requires replacement, removing the need for any specialized testing.
OSC – advanced technology for all compressed air condensates
The new and extensive OSC range from Atlas Copco uses patented technology to separate all kinds of compressed air condensate. The multi-stage separation process, using both buoyant oleophilic filters and activated carbon, ensures exceptional performance, long and known filter lifetime and trouble free operation.
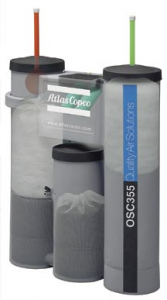
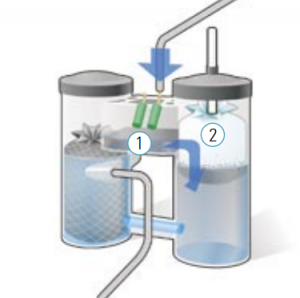
Complete reliability from total simplicity
1 Condensate enters through the mufflers and depressurizes in the expansion chamber.
2 The emulsified oil-water mixture then enters tower A and seeps through the white oleophilic filter. The filter absorbs the oil but not the water.
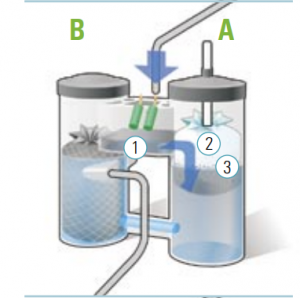
3 The oleophilic filter floats on the water and absorbs any remaining oil from the surface.
The additional weight of the oil causes the filter to gradually sink as it gets more saturated, which ensures that clean filter material is always in contact with the surface of the water.
The indicator stick at the top of tower A shows the status of the filter; as the filter is consumed, the stick sinks. The filter has to be changed just before it’s fully submerged
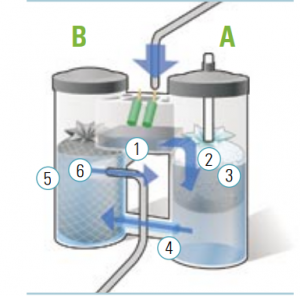
4 Significantly cleaner condensate flows from tower A to tower B.
5 Tower B contains a bag of activated carbon pellets (contained in a bag) which absorb any residual oil from the condensate.
6 Clean condensate exits from tower B with almost no residual oil content, enabling it to be discarded easily and safely.
Capacity is based on the compressor running at 7 barg / 100 psig for 12 hours per day, with all condensate from the compressor, the air receiver and filters being piped into the unit.
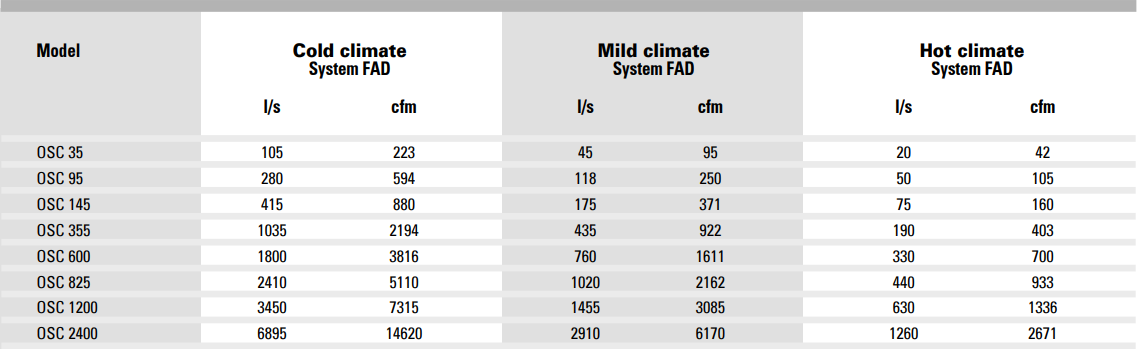
Notes
1) All capacities are based on an outlet oil content of 15 mg/l.
2) Climatic conditions used in the table above are defined as follows:
- Cold conditions: ambient temperature 15°C relative humidity 60%
- Mild conditions: ambient temperature 25°C relative humidity 60%
- Hot conditions: ambient temperature 35°C relative humidity 70%
3) For poly-glycol based condensates, the capacity of each unit should be halved.
6231644600 | GASKET, AFTERCOOLER, | 6231-6446-00 |
6231644500 | GASKET SEPARA. D258 | 6231-6445-00 |
6231611300 | KIT-SERVICE | 6231-6113-00 |
6230578865 | CD-ROM QRS/CPVS 15 T | 6230-5788-65 |
6230548565 | CD CPE-CPVS 75-150E | 6230-5485-65 |
6230548465 | CD-ROM CPD | 6230-5484-65 |
6230548265 | CD CP 40-75 CHICAGO | 6230-5482-65 |
6230521600 | AUTOCOLLANT ALIMENTA | 6230-5216-00 |
6229046900 | KIT DESHUILEUR RLR 4 | 6229-0469-00 |
6229046800 | KIT DESHUILEUR RLR 6 | 6229-0468-00 |
6229043000 | KIT PRESSURE QRS30 1 | 6229-0430-00 |
6229042900 | KIT PRESSURE QRS25 1 | 6229-0429-00 |
6229042800 | KIT PRESSURE QRS20 1 | 6229-0428-00 |
6229042100 | KIT PRESSURE QRS30 1 | 6229-0421-00 |
6229042000 | KIT PRESSURE QRS30 1 | 6229-0420-00 |
6229041900 | KIT PRESSURE QRS30 1 | 6229-0419-00 |
6229041800 | KIT PRESSURE QRS25 1 | 6229-0418-00 |
6229041700 | KIT PRESSURE QRS25 1 | 6229-0417-00 |
6229041600 | KIT PRESSURE QRS25 1 | 6229-0416-00 |
6229041500 | KIT PRESSURE QRS20 1 | 6229-0415-00 |
6229041400 | KIT PRESSURE QRS20 1 | 6229-0414-00 |
6229041300 | KIT PRESSURE QRS20 1 | 6229-0413-00 |
6229038700 | KIT 8000H CPC 60 (ON | 6229-0387-00 |
6229038600 | KIT 8000H CPC 50 (ON | 6229-0386-00 |
6229038500 | KIT 8000H CPC 40 (ON | 6229-0385-00 |
6229038300 | THERMO VALVE 83C C77 | 6229-0383-00 |
6229038200 | KIT 8000H QR | 6229-0382-00 |
6229038100 | KIT 8000H QRS/CPVS 2 | 6229-0381-00 |
6229038000 | VTH 85C CPVS 60 A75 | 6229-0380-00 |
6229037900 | TROPICAL THERMOSTAT | 6229-0379-00 |
6229037700 | KIT REMONTAGE ENGREN | 6229-0377-00 |
6229037600 | KIT REMONTAGE 脡L脠MEN | 6229-0376-00 |
6229037500 | KIT CPD100 175PSI | 6229-0375-00 |
6229037400 | KIT CPD100 125PSI | 6229-0374-00 |
6229037300 | KIT CPD100 100PSI | 6229-0373-00 |
6229037000 | KIT CPD75 100PSI | 6229-0370-00 |
6229036900 | KIT CPC60 175PSI | 6229-0369-00 |
6229036800 | KIT CPC60 125PSI | 6229-0368-00 |
6229036700 | KIT CPC60 100PSI | 6229-0367-00 |
6229036600 | KIT CPC50 175PSI | 6229-0366-00 |
6229036500 | KIT CPC50 125PSI | 6229-0365-00 |
6229036400 | KIT CPC50 100PSI | 6229-0364-00 |
6229036300 | KIT CPC40 175PSI | 6229-0363-00 |
6229036200 | KIT CPC40 125PSI | 6229-0362-00 |
6229036100 | KIT CPC40 100PSI | 6229-0361-00 |
6229035400 | KIT CPD100 150PSI | 6229-0354-00 |
6229035300 | KIT CPC60 150PSI | 6229-0353-00 |
6229035200 | KIT CPC50 150PSI | 6229-0352-00 |
6229035100 | KIT CPC40 150PSI | 6229-0351-00 |
6229031700 | KIT NON RETURN VALVE | 6229-0317-00 |
Post time: Jan-16-2025